Home > Show Us Yours! > My ever lasting project
|
mini93

834 Posts
Member #: 2017
Post Whore
Warwick.
|
|
Thought I may aswell start up a project on here seeing as im now moving on toward the turbo route.
I've owned this mini since 2007 and gone through some different routes in a rather small amount of time. Its also been off the road more than been on it since iv owned it, so this is the new route and doing it propperly!
I bought it off some guy through a friend with the intension of rallying it, the previous owner turned out to be a complete arse, claimed engine builder. The car was a bit of a shambles, but unfortunatly only noticed this after I had bought it.
The engine being a 1330, 286 cam, ported head, weber 40, ultralite steel flywheel and back plate and sold running on a JKD dog engagment dog box, open diff with a mear hardened diff pin.
So with the intension of rallying it, I spend a butt load of money doing all my tests, getting my overalls etc
The rally I chose was emerald stages, a single venue event at rockingham... and was a disaster. 1st stage my co-driver accidently sent me the wrong way at a split, I gathered stage maximum. 2nd stage, the fun began.
I managed to do over half the stage, going the correct way at the split this time. Suddenly I noticed that my oil pressure light was on. I retired on stage 2 (and that is currently as far as my rallying career has got)
Upon removal and dismantling the engine I find many problems with the engine.
The route cause of the low oil pressure was the bottom drop gear bearing was not fitted correctly. This sent the drop gear away from its seat, spinning into the casing sending swarf into the oil, ruining the oil pump and bearings
The gearbox was dismantled by Southam mini and metro centre as a matter of course to check the condition. It was found that the layshaft was fitted mearly with a brass bush instead of a roller bearing!!! (the delivery of the car was delayed because apparently the previous owner couldnt find the correct bearing, apparently finding one and rebuilding the engine)
The diff was also found to be 75% the way through the harded diff pin.
The compression ratio of the engine was also up at 12:1 or so. This then lead to det and failure of the piston ring land
Rather disheartening :( this car wasnt turning out to be as great as Id hoped.
The engine was rebored and rebuilt using 73mm pistons (1362cc) and using a 286 scatter cam, sc-drop gears, x-pin diff. and built up with megajolt.
The car also went through a bit of a change. decided I wasnt going to rally a mini anymore, chopped open the front bulkhead to fit a miglia style bulkhead, new fibreglass dashboard rather than the bland dash it had before and a re-colour away from the blue it was sold to me with.
Not without its problems, I was rushing to get the car ready for castle combe action day, got an MOT by phone but still failed to make it there. later inspection of no oil pressure on cranking, the new oil pump which i had fitted had managed to snap the drive jack...infuriating and again very disheartening.
Getting a bit bored of using the car while it actually worked >_<
I chopped the front end off in faviour of a fibreglass clubman front
This is pretty much how it worked for most of the time.
Did a few blasts at Avon and santa pod, managing a 15.9 in a rather heavy weight trim.
David.
|
WRLondon

1170 Posts
Member #: 8636
Post Whore
Surrey
|
|
Nice
Know exactly what you mean about people messing about with minis and claiming its immaculately modified but more just majorly bodged!
Will keep an eye on this one :)
Edited by WRLondon on 28th Apr, 2013.
Reading up on RTS Clutches On 21st Sep, 2006 Paul S said:
Go on, be brave, put it in the car and tell us how it works.
Pity your bollocks are in line with the flywheel! On 27th May, 2013 robert said:
putting my testicles on the line for turbo mini owners everywhere ,and they still work !
|
mini93

834 Posts
Member #: 2017
Post Whore
Warwick.
|
|
Fast forward to Avon park of 2010, I manage to make it there finally with a funtioning mini!
But as ever with this car, it chooses not to go to plan.
Even though it has a grey diaphragm fitted and utilsing a 190mm paddle clutch I suffered with clutch slip within the 1st 200 yards of setting tyre on the track.
I still make my way round for the slot, but assume the faults down to the oil seal weeping as the clutch combo should be more than man enough for my application.
With the tax out on the mini I decide to lay it up, assuming ill do a few small jobs over winter and will be back in the spring before my target of Riviera run 2011.
The mini came off the road to have a reshuffle of the rear end, a little bit of lightening, some suspension rejigging.
I was going to lower the car, so set out my chopping into the rear 1/4's and greeted by a lovely sight
and it has very much snowballed from there.
New rear 1/4's went into the shell. I aso purchased from e-gay a minispares alloy beam aswell as Kad alloy radius arms aswell as a few other bits n bobs.
Turning into more of a full rebuild the car was stripped down and put on stands.
The car was now heading for lighter route. The car lost the roof and rear bulkhead in faviour of lighter items. The front bulkhead was again removed to be made from lighter stuff.
Eventually the shell headed off to shot blasting
Showing alot of work required, the rear of the boot floor was chopped out, the arches were removed. These would be replaced by new items.
The new arches were fitted along with some JB fabrication turrets
I had some hold on the floor where its been battered in its previous life as a rally car, these have all now been welded up
It sat very well in bare metal over a very cold winter. it hasnt rusted too badly, only a bit of surface rust.
I will still be getting the shell blasted again prior to paint.
So as it sits now...
Another problem with the car being the rollcage. On the face of it, it was rather substancial. following the strip down and the blasting it was apparent this was not the case.
The person who welded was a complete monkey. half the tubes weren't welded the full circomfrance of the tube leaving a weak joint.
At this point i decided to go a more convensional route with the rollcage. chopping it out past the B-hoop and going down to the rear turrets with a traditional x-bar with intergrated harness bar.
The front and rear bulkhead to be fabricated from aluminium.
Back to the rollcage, most of the problems were on the front foot-well triangulation
Looking through a hole in the inner wing I cut.
While the car was on the side the sills were chopped out to be replaced with new ones, which is a good thing i decided to as i found that the sill stand tubes were only welded to the outter sill and not the inner, so rather weak. These will now be replaced.
I also decided to replace the door post/inner wing section aswell as the scuttle gusset, it was a little crusty. Iv decided that ill do all the pain in the arse body work and wont need to do it again in a hurry!!
So, onto todays work. finally putting into motion the turbo route I took the grinder to yet another part of the mini and chopped the bulkhead out for the turbo box
Future plans with the car will be to complete all the panel work. The shell will then go for the pre-primer shot blast. After its been primered Im going to get the car back and do a complete dry build I dont want to be drilling holes into the fresh paint so everything will happen in the primer stage, then I will take everything apart again and send it off. The full wet build should be quite quick after that (or so I hope!)
I havent got a lot yet for the turbo route, I have obtained a turbo carb and a nic-plenum... not exactly a long list, but I still have plenty of time to obtain more engine bits while the build continues
Thats a very cut down history of my mini... missed out a fair amount of detail but heres where the boosted fun starts
Edited by mini93 on 28th Apr, 2013.
David.
|
apbellamy

16540 Posts
Member #: 4241
King Gaycharger, butt plug dealer, Sheldon Cooper and a BAC but generally a niceish fella if you dont mind a northerner
Rotherham, South Yorkshire
|
|
Looks good. I feel your pain for all the botched body work. I had lots of the same with my car.
On 11th Feb, 2015 robert said: i tried putting soap on it , and heating it to brown , then slathered my new lube on it
|
mini93

834 Posts
Member #: 2017
Post Whore
Warwick.
|
|
Thanks, Its a pain, im really not a body work kinda guy so its a do it once right kinda situation.
things go slow sometimes just because its a residential area. Last Saturday I didnt get any work done because it was the 1st warm sunny day of the year and didnt want the complaints to pour in.
I should recieve the sill stand kit this week then I can throw the new sills on, flip the car on to the other side and continue with the o/s.
That will be the mass of the panel work that will need welding in then. after that I can do all the rollcage modifications and that should just about see me at primer stage.
David.
|
Turbo Phil
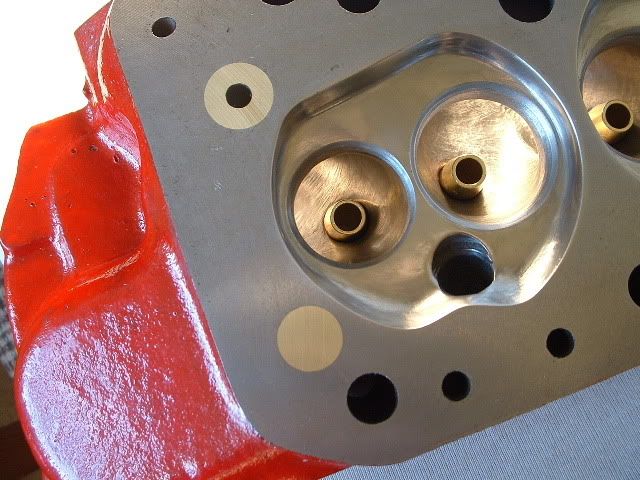
4625 Posts
Member #: 20
My sister is so fit I won't show anyone her picture
Lake District
|
|
Looks like a lot of hard work, good effort so far.
WWW.TURBO-MINI.COM
|
mini93

834 Posts
Member #: 2017
Post Whore
Warwick.
|
|
Thanks Phil, yes, alot of work so far... but keeps me busy! and as much as I dislike doing body work I'm sure there will be major project completion syndrome when im done.
So a few bits arrived before i headed to Riv run last week. I also got a couple of extra days off work as i was unsure if I was staying down south so decided to just use them as garage days instead of going back to work right away.
The shell was fitted with sill stands when i bought it. however when i took the sills off to replace them, i found that they werent fitted very well and the rear sill stands werent even welded to the inner sills.
So completly unhappy with it, I chopped these out to replace them
I got new ones from Peter Lloyd and while they arent exactly on the scheme of lightening things, they make working on the car simpler, safer and lifts it to a good height to work under where required.
They came with the stands, tubes and bits.
I decided that the supplied plate, which usually goes on the outside of the sill was better placed on the inside of the sill to add strength. I will make another plate for the outter sill.
So to fitting the new tubes, checked and doubly double checked that the tubes were level in the car. (checking against a known level bar of the rollcage)
Bit of a pain getting weld on the full circomfrance of the tube, but its in place.
Both tubes on the N/s now fitted and only roughly chopped down. Decided to see how much space under the car the stands will provide. It should be quite comfortable under there!
So that is where its sitting at the moment.
Thinking towards the outter sills, fittment and getting holes I decided to grab a holesaw set.
Seems like a nice set from Titan. It will also help with the lightening fetish
So before the sills go on, I will patch up the original jacking point and the redundant holes, mark up and holesaw the sills to allow for the chassis stand tubes.
Im hoping I manage to get the sills on tomorrow, this will allow me to flip the car onto its other side and maybe even start chopping the o/s sill off.
Cheers!
David.
|
mini93

834 Posts
Member #: 2017
Post Whore
Warwick.
|
|
So I did a bit today, the near side is almost completed now, just a few more bits to do. pics will show over.
Started up by throwing a bit of paint on the inside of the sills, its probably not the most protective of jobs I could have done, but its better than just the plain ol' steel that was on there before.
Simple black up!
Black always seems to make some things neater.
After that I prepped the sill, welding up the redundent holes and the original jacking point... clamped up and welded on
Looking pretty swanky at the join with the sill stand poking through.
Today I bought the last of the new panels that need to get welded in place, the off side door post section repair panel and the scuttle closing gusset.
after that i set out working on the mini and finishing off on the near side.
I first of all plated up some remaining holes, these were into the rollcage foot box section so were missed when i welded up the holes from the inside.
with that done i moved onto finishing the sill stands up. Made a plate for the outside of the sills using a bit of CAD (cardboard aided design) transfered to metal and bosh, welded up.
Its not the neatest job, i still find moving round a tube a bit tricky when welding continiously so I used the pulse weld method.
just needs a little tidying up with a die grinder when i have access to one as the space is too tight for the grinder to get into.
After that it was time to flip the mini back correct way up. but only for a short while. soon ill be flipping it back on its side to weld up the off side.
I've still got the bulkhead to finish off, but the majority of it is there now so shall crack on after the other sill etc is completed.
Just to show whats to do on the nearside
Door post being a bit crusty this will be chopped and re-done. The holes i've already chopped in the panel grant a lovely view of the shit welding on the rollcage, pictured below.
and also the scuttle closing panel.
these will all get fixed in their respective ways and also ill replace the offside sill.
Then before it can stay correct way up, i have to re-make the exhaust tunnel section i chopped out.
Its getting closer though
David.
|
mini93

834 Posts
Member #: 2017
Post Whore
Warwick.
|
|
Bit more of an update now.
I've had the car on its side for a few weeks and had a few weekend to crack on with the car.
On its side waiting for the work to coninue.
First on the list for this side was to remove the near side sill. It would allow me to remove the old sill stand tubes, assess the heel board mounts and then move onto the inner wing.
Wasnt a very neat removal, I was a bit of a butcher in places and chissled off the strengthening brackets rather than drilling the spot welds out... But at least its done. just a few holes to patch up.
With the sill off I was able to see that the original heel board mounts had been drilled out and re-tapped (not very well) so decided to use the replacment panel I had already purchaced to fix this.
This is as far as I have got with repairing the panel for the moment. I threw out the old subframe bolts when I disassembled the car so awaiting new shiney ones before I progress further with this. This will allow me to bolt the new panel up to my mini spares alloy beam and ensure i get the correct positioning.
Onto today I was tacking the front end and the inner wing/door post.
The above is the original... very holy and seeing as I replaced the n/s I thought id do this side aswell.
All removed I was able to get at the shit footwell triangulation and the lack of welding
I dont know how anyone would be happy fitting this cage to the car knowing full well that it hadnt been welded fully, either for personal use or even more so if it was built for a customer!
So I welded that up...not the neatest of welding as it was difficult to clean up the join, but im happy with it, I gave the 1 weld I could get to a light dressing with the grinder afterwards.
And as if by magic... A long drawn out magic which took ages to prep.
I took a bit more time welding in the new panel than I did welding in the N/s one. I had a bit of warpage last time.
I havent got round to grinding it back yet though. I've still a few more bits and pieces to weld up on the inner wing before that.
I also got a little something to progress the turbo side of the build.
I bought Sumpnuts old cylinder head. Should be good starting point for the engine for when i eventually get round to building it.
Hopefully I will be able to finish off the inner wing next weekend and move onto finishing the heelboard
David.
|
jakejakejake1

293 Posts
Member #: 10010
Senior Member
Northants
|
|
Good work, at least you know there will be no more bodges from here on out!
|
mini93

834 Posts
Member #: 2017
Post Whore
Warwick.
|
|
Thanks and yes, thats the idea. Will take a bit longer than id like (and already has been too long) but it should be just how i want when iv finished.
Got a quick 1/2 hour on the car after work this evening the inner wing not being ground back was bugging me so i had a whirl at that. looking much better and less warped than the near side.
Will see if I manage to get any time this weekend!
David.
|
mini93

834 Posts
Member #: 2017
Post Whore
Warwick.
|
|
So, the new replacement heelboard panel is sh*te... went to bolt it upto my mini spares beam and the holes didnt line up! fantastic eh!
So thinking in the week the best way round it would be a simple chop down the middle and weld back together.
Looks a long way out, but thats with the cutting disk thickness aswell.
It was easily bridged using some brass behind it
I also added a bit more weld behind the captive nuts, last thing I want are for them to come free/spin
After that, a bit of fettling and I got the repair panel in place
Just double checking that they stil alined and bolted up, thankfully they did!! (mostly. it was a bit tighter than I would have liked but thats sorted at least. Just need to dress the weld on the outter heelboard when I get access to a compressor and die grinder.
After that I moved onto sorting the o/s sill stands. much the same as I did before
Managed to control my shakey jake hand for the majoiry of this strenthening plate, still had a little bit of a dress afterwards
Rear done
So all welded in there, just a case of hole-sawing the outter sills up and fitting them on.
Iv still to finish off the inner wing, still to do a few patches, fit the scuttle gusset and few small odds n sods and thats this side completed, then it can go back onto its wheely trolley again.
David.
|
Nic
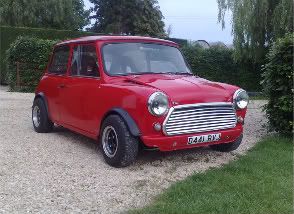
9317 Posts
Member #: 59
First mini turbo to get in the 12's & site perv
Herefordshire
|
|
Nice work!!!
I wish I put some of those sill stands on my car
|
mini93

834 Posts
Member #: 2017
Post Whore
Warwick.
|
|
Cheers nic,
They are usefull, especialy when evenitbly work needs to be done. Dont really sit in your line of light weight though.
David.
|
BENROSS
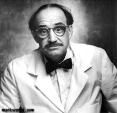
9812 Posts
Member #: 332
Resident Cylinder Head Modifier
Mitsi Evo 7, 911, Cossie. & all the chavs ...... won no problem
|
|
good work so far, keep at it.
it will be worth all the hard work in the end
|
Rob Gavin

6729 Posts
Member #: 618
Post Whore
Glasgow
|
|
you look like your covering ground quickly; I think it took me 3 years to get to this stage!
|
mini93

834 Posts
Member #: 2017
Post Whore
Warwick.
|
|
Thanks guys,
its not really as quick process as iv may seem.
The car was last on the road in 2010 after coming off the road following Castle Combe mini action day. horrible clutch slip and a few jobs to do to the car I was going to take it off the road for winter and bring it back on the road for May's Riviera run.
Only starting work on the car in circa feb/march, discovering I wasnt going to be able to simply tub the rear arches due to cronic filler issue, the strip down began.
And its pretty much evolved off there, along the way it was an everything out and shot blast affair. super lack of enthusiasm not a whole lot got turned around in 2012.
Hit a bump when my friend required his welder back and being a stuborn bastard I refuse to use a hobby welder after getting used to an indistrial type welder with decent gas. Took me a while to get around to getting my own welder around the beginning of this year and yet even more time to get round to getting a gas supplier. All this in hand Iv been getting on with it steadily.
I could still work at it harder though, I rarely go to the garage after work (which i keep telling myself I should do) and I give myself an excuse of not working on the car early on the weekends because of the noise and neighbours, 1 of which im thinking is boarder line phycho.
Still, I push
David.
|
mini93

834 Posts
Member #: 2017
Post Whore
Warwick.
|
|
Got a chunk more done.
Thought I saw the begining of the end of the body work. But its still a while away it appears
Anywho, pictures. Got the inner wing finished off
Bit of an ackward panel to patch up, bends in 3 direction even just slightly
Got that welded up and also patched the hole where the fresh air vent used to be. I also welded in the scuttle closing panel.
Next I moved onto the new sill.
Welded onto the parent sill
All welded up. Strengthening plates welded onto the sill and around the sill stands.
Again i really need to get myself a compressor so i can use a die grinder to get into the hard to reach areas. just more money I could be spending on brum brum stuff.
So with the new heel board repair section, sill, sill stand tubes, inner wing and scuttle closing panel finished on the near side and the o/s completed previously I wanted to see how the car sat on the new sill stands. The floor isnt really finished off yet. I think I would be best having the car on the side to finish off the exhaust tunel replacment, but i havent got hte steel at the moment and I was too nosey to see how high the car sat up on the stands
Its high alright! Deffinatly going to need to get myself a decent jack now!
As I said before, the floor isnt finished yet untill the exhaust tunnel is welded up. I just need to remember to get some delivered to work.
In the mean time I still need to dress the inner wing repair welds from the inside. ensure there are no pin holes. These will still get a coat of seam sealer just in case.
Anywho, thats all for now...
David.
|
mini93

834 Posts
Member #: 2017
Post Whore
Warwick.
|
|
A bit more progress on the shell (some of it not so recently)
Been cracking on at making the floor complete.
Previously the exhaust tunnel had been widened for what ever reason, assuming ground clearance. I originaly cut it out because it was a bit of a patch work quilt of panels, looked a bit gash so chopped that out.
I then decided to revert back to a standard width, without wanting to buy expensive replacment panels I made my own.
Just to show what I was up for, big ol' hole.
Bit of a task to get the bend in the correct place to go back to standard width, it wouldnt fit in the bender that I have.
Starting the fit, realised I still had a small gap in places, easily fixed with a few small fill in bits
Fully welded from the inside, still need to dress the welds and some more in the inside.
After flipping the shell onto its side again and seam welding the panel all round, this was what I ended up with. Rather pleased with the results.
Another angle. The tunnel is a full round type, rather than flat top as I will be using an internal gear linkage, so i dont need the flat section for it to fit through.
So with the floor completed I had a little bit of time just to seam weld the turbo box in place. It was looked a little bodged in place being simply spot welded in place, looks a lot better being seam welded and im sure much stronger too.
Anywho, thats all for now! Hopfully I wont leave it as long next time.
David.
|
afrance2905
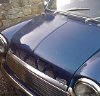
265 Posts
Member #: 10512
Senior Member
whitby, north yorkshire
|
|
looks good, been following on the other forum, im going to be doing the same with the sills
|
mini93

834 Posts
Member #: 2017
Post Whore
Warwick.
|
|
Its a good mod with the sills, seems to be the one everyone think's will be most useful.
Just have to remind though, that they do stick a way into the car (past the inner sills)
As I have a rollcage mounted onto boxes, the stand tubes sit up against this (and will be welded to it eventually) Without a cage or anywhere to tie it to on the inside, it might be a bit intrusive and look odd.
David.
|
Sprocket
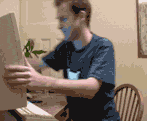
11046 Posts
Member #: 965
Post Whore
Preston On The Brook
|
|
If this the actual car, I remember commenting to Grace and Ali about the intensity of that cage at the Mini show in the NEC back in, ooh, must have been 1997. The car looked alot straighter then lol not long after they bought it from Minisport with a student loan lol.
How bizzar you are cutting it about lol.
On 26th Oct, 2004 TurboDave16v said: Is it A-Series only? I think it should be...
So when some joey comes on here about how his 16v turbo vauxhall is great compared to ours, he can be given the 'bird'...
On 26th Oct, 2004 Tom Fenton said: Yep I agree with TD........
|
mini93

834 Posts
Member #: 2017
Post Whore
Warwick.
|
|
I funnily enough spent quite a bit of my student loan on it aswell.
And I know, I know... I like to ruin history but to be honest, the shell wasnt peachy when i started digging away. The rollcage was very poorly welded, it was only good to look at in the places it was easily visable to scruteneers etc, so iv been going over the badly welded joints (including cutting access though the inner wing) welding the bits that were missed and the bits that were welded badly, grinding back the surface "dressing" and then using a higher power ensuring there actually is penitration.
I know for sure the cars been rolled before and the cage has survived, but theres nothing to say it would next time.
As for the modification to a more conventional rollcage style, there must be a reason why most other rollcages you see put into vehicles go straight down after the B-hoop rather than following over the top of the body to the C-piller and down. So I'm just going for a tried and tested route, it will be lighter and the rear stay on the N/S was bent away from its mounting position on the rear arch, so that in itself needed more attention than I wanted to give it.
David.
|
mini93

834 Posts
Member #: 2017
Post Whore
Warwick.
|
|
So talking about the rollcage.
I got on with modifying it to a more conventional style
This is what it was originaly. Up along the roofline to the C-piller and down onto the arch.
Bit of a chop later...
Keeping the lower rear stays to mate to the rear stays off the top of the B-hoop down to the arch turrets.
So as i think i mentioned before, the welding was shit... But just to show how bad
Showing the lack of penitration on the tube wall to the original B-hoop mounting.
and from the other side you can see how ferious the weld was showing little wall penitration.
To get round this on other parts of the cage, I've turned the current very high on the welder and wire feed down, melting the original weld without adding too much material.
Not the neatest of jobs, but a quick dress of the welds will see it looking better.
I've also done a bit of patching and finishing on the front bulkhead. cutting and plating the master cylinder holes as ill be going internal box.
bit of seam welding between bulkhead and cross member.
plating the redundant scuttle panel holes
But, when I thought I had no more rust, I found what I hope to be the last of it.
The o/s shock mounting, bit scabby! lovely eh!
Anywho, thats all for now.
David.
|
Rammie2000
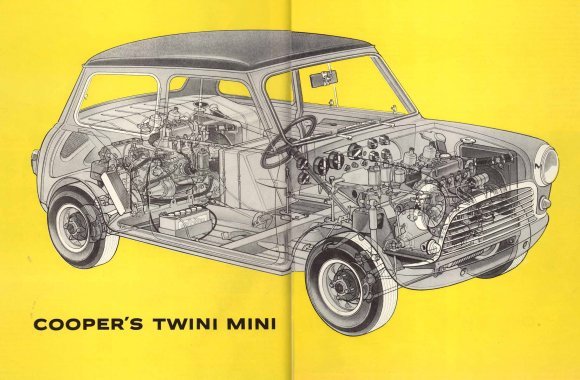
1750 Posts
Member #: 10190
Post Whore
belgium
|
|
Yep had the same here... tought on making some brace bars... pulled away the towers.. and woop there it is... but don't loose courage your almost there.
you can do anything if you set your mind to it...
i rather blow it up winning than keep it together losing.
finish date set for project 1... march 2018
|
Home > Show Us Yours! > My ever lasting project
|
Users viewing this thread:
none. (+ 4 Guests)
|
Next ->
|
|